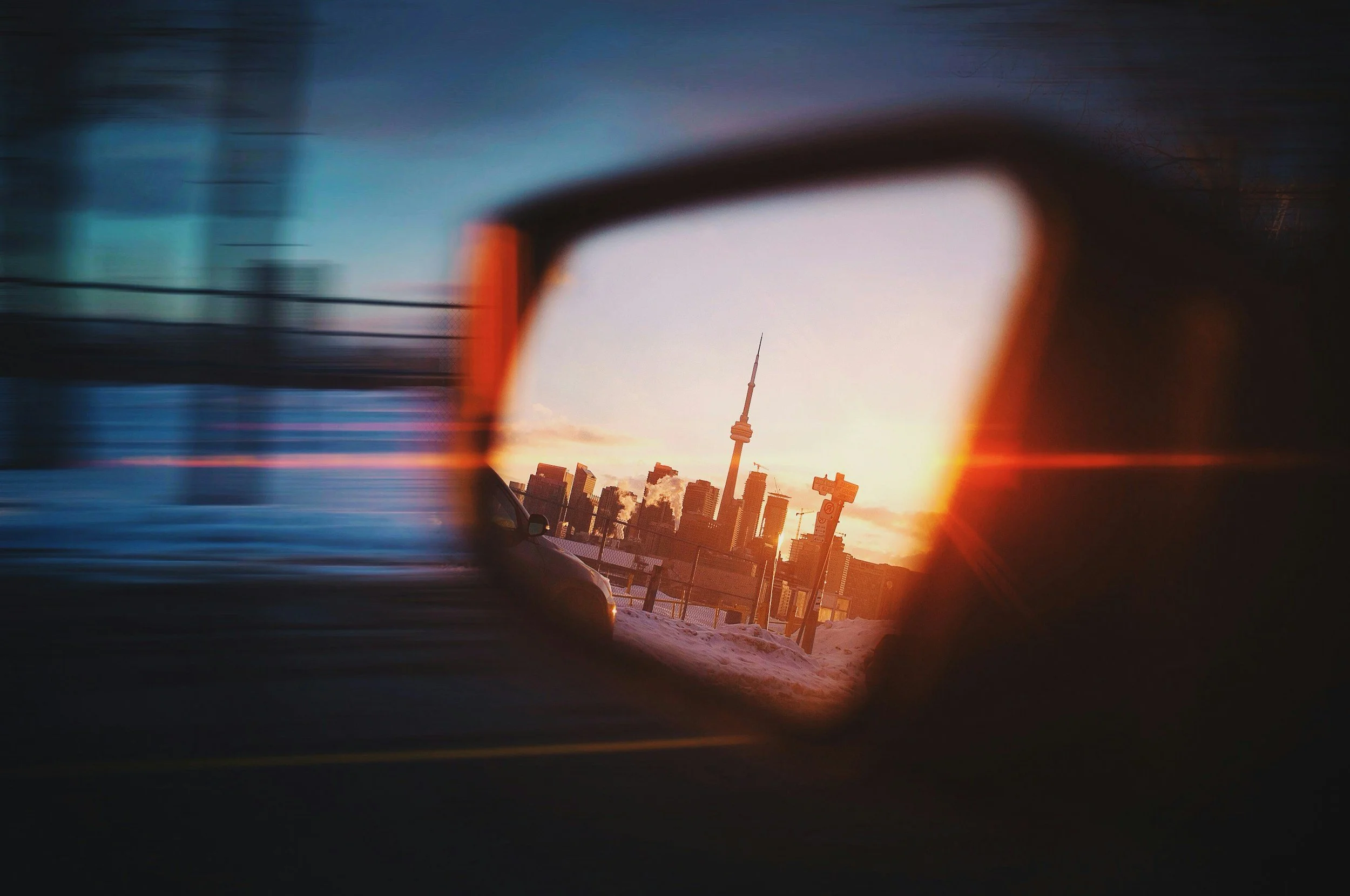
HDPE Liners vs. Epoxy: Best for Concrete in Toronto?
When it comes to protecting concrete structures, choosing the right method is critical. In Toronto, where varying weather conditions and industrial demands put enormous stress on concrete, selecting an effective protection solution can make all the difference. Two popular options are High-Density Polyethylene (HDPE) liners and epoxy coatings. Each has its own set of advantages and challenges, which makes understanding their differences essential for making an informed decision.
Durability and Longevity: HDPE Liners vs. Epoxy Coatings
Durability and longevity are crucial factors when it comes to protecting concrete. Epoxy coatings are known for providing a hard, durable surface layer over concrete structures. They can withstand significant wear and tear, making them suitable for many industrial applications. However, their rigidity can be a downside. Epoxy tends to crack and chip over time, especially under Toronto's fluctuating seasonal temperatures. The freeze-thaw cycles cause the concrete to expand and contract, leading to the early deterioration of the epoxy coating.
In contrast, HDPE liners are designed for enhanced durability and flexibility. HDPE, or High-Density Polyethylene, is inherently flexible, allowing it to accommodate the natural movements of concrete. This adaptability makes HDPE liners less prone to cracking and other forms of degradation. They perform exceptionally well in environments with extreme temperature variations, providing consistent protection throughout their lifespan. Additionally, HDPE liners have a lifespan that often exceeds that of epoxy coatings, reducing the need for frequent replacements and repairs.
The ability of HDPE liners to maintain their integrity over long periods makes them a superior choice for concrete protection. By avoiding the common pitfalls of rigid coatings like epoxy, HDPE liners offer greater overall resilience, ensuring concrete structures remain protected and functional for many years.
Chemical Resistance: Why HDPE Outperforms Epoxy
Concrete structures in industrial settings are often exposed to a variety of chemicals. The protective material's ability to resist these chemicals is paramount in determining its effectiveness. Epoxy coatings do provide a certain level of chemical resistance but can degrade when exposed to harsh substances over time. Acidic or alkaline environments can cause epoxy to lose its protective properties, leading to surface erosion and potential structural damage.
HDPE liners excel in chemical resistance. These liners are designed to form an impermeable barrier, effectively shielding concrete from a wide range of corrosive chemicals. HDPE is resistant to acids, bases, solvents, and other harmful substances commonly encountered in industrial settings. Unlike epoxy, HDPE does not degrade when exposed to these chemicals, ensuring long-term protection.
For industries in Toronto, where chemical exposure can be a daily challenge, HDPE liners provide a reliable solution. Their superior chemical resistance helps maintain the integrity of concrete structures, reducing the risk of chemical-induced damage. This protective capability makes HDPE liners a preferred choice for applications where chemical exposure is a significant concern.
Installation and Maintenance: Comparing Costs and Efforts
When considering concrete protection methods, it's important to understand the installation and maintenance requirements, as these factors influence both time and cost. Epoxy coatings generally offer a straightforward installation process. The surface is cleaned, primed, and then the epoxy is applied. However, this process can be labour-intensive and time-consuming. Additionally, curing times for epoxy can vary, often requiring several days before the surface can be fully utilized. This waiting period can result in prolonged downtime for industrial operations.
Maintenance of epoxy coatings is another factor to consider. Although they provide a durable surface initially, they can suffer from wear and tear over time, necessitating regular inspections and repairs. Cracks, chips, and peeling may require patching or re-coating, adding to the long-term maintenance costs and efforts.
On the other hand, HDPE liners provide a more efficient installation process. These liners are typically cast into the concrete during the precast process at the producer, reducing the overall installation time. They may also be applied to the formwork during cast in place applications. Once in place, HDPE liners require minimal maintenance due to their resilience and flexibility. They don’t crack or peel, even under extreme conditions, which significantly lowers the need for frequent repairs. The long-lasting nature of HDPE liners translates into reduced maintenance costs and efforts, making them a more cost-effective solution over time.
Environmental Impact: Sustainable Choices for Concrete Protection
Sustainability and environmental impact are increasingly important considerations in industrial applications. Epoxy coatings, while effective, can present environmental challenges. The production of epoxy involves chemicals that can be harmful to the environment. Additionally, the disposal of epoxy materials, once they have degraded, poses another environmental concern. Epoxy coatings also require frequent replacements, contributing to waste and the environmental footprint.
HDPE liners, in contrast, offer significant environmental benefits. HDPE is a recyclable material, meaning that at the end of its lifecycle, it can be reprocessed and used again. This recyclable nature supports sustainability and reduces the carbon footprint associated with material disposal. Moreover, the long-lasting durability of HDPE liners means fewer replacements and less waste generated over time.
By choosing HDPE liners for concrete protection, industries in Toronto can align with environmental sustainability goals. The reduced need for repairs and replacements, along with the material’s recyclability, make HDPE liners an eco-friendly choice. Protecting concrete structures while minimizing environmental impact is an achievable goal with HDPE liners.
In the quest for the best concrete protection solution, understanding the advantages and limitations of both HDPE liners and epoxy coatings is crucial. HDPE liners stand out with their superior durability, excellent chemical resistance, and minimal maintenance requirements. These liners offer long-term protection for concrete structures, particularly in challenging environments like those found in Toronto. Additionally, the sustainability benefits of HDPE—thanks to its recyclability and reduced need for replacements—make it a preferable choice over traditional epoxy coatings.
Selecting the right material is essential for extending the lifespan and safety of your concrete structures. HDPE liners provide a robust, reliable, and environmentally conscious option that outperforms epoxy in many critical areas. Making an informed decision based on these factors can lead to significant long-term benefits and cost savings.